Igen izgalmasnak találtuk a menetpróbán személyesen is megismerni az MAN TG-család temérdek újdonságát. Ám legalább ennyire érdekes bepillantani a fejlesztési, a tesztelési, valamint a gyártás-előkészítési folyamatába.
Ötévnyi megfeszített munkába telt, mire a papírra vetett első ötletekből a sorozatgyártásra kész tehergépkocsi-család testet öltött. Az MAN az elmúlt húsz év legjelentősebb projektjét hajtotta végre, amelyre a vállalat 2100 munkatársa összesen 12 millió munkaórát fordított.
A müncheni központ szigorúan őrzött innovációs központjában 360 mérnök egy 33 ezer négyzetméteres területen dolgozott az új járműveken. Habár ebben a 2015 májusában útjára indított projektben a TG-család külső megjelenése, a fülkék belsőterének és vezetőállásának kialakítása, valamint korszerű vezetéstámogató rendszerek bevezetése állt a középpontban, az oroszlános tehergépkocsikat számos más, kevésbé szembetűnő ponton is továbbfejlesztették.
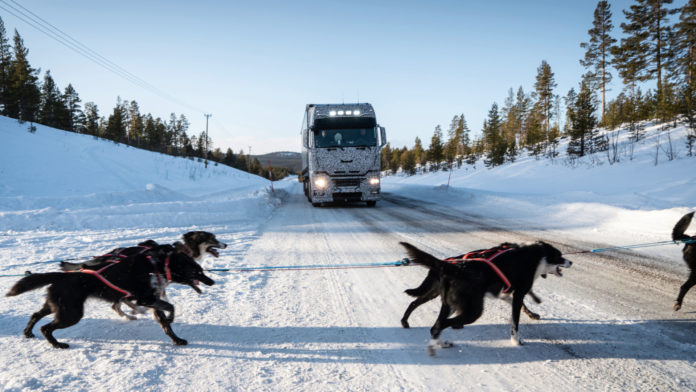
Fokozott tartósság
Tartóssági tesztek eredményei alapján megerősítettek, illetve átterveztek olyan elemeket, mint például a hűtőradiátor egyik tartókonzolja. Ezenkívül a klímaszimulációs laboratóriumban is lázasan folytak a legkülönfélébb alkatrészek szélsőséges hőmérsékleti és más környezeti viszonyok közötti tesztjei. A fejlesztők úgy optimalizálták az alkatrészeket, hogy azok legalább 1,2-1,5 millió kilométert kibírjanak. Persze nemcsak belső vizsgálatokból származtak a továbbfejlesztési feladatok, hanem az ügyfelek tapasztalataiból és javaslataiból vagy éppen a közeljövőben várható jogszabályi módosításokból is, mint például a 2021-ben életbe lépő szigorúbb ütközésbiztonsági előírások.
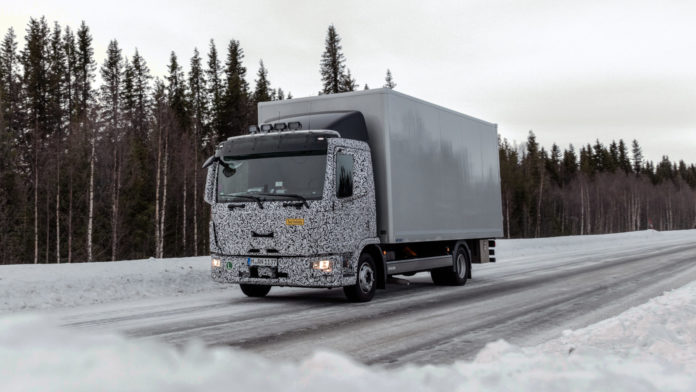
Rázós tesztek
Már 2017 májusában elkészült az új tehergépkocsik első prototípusa, és ezt követően maguknak az álcázott járműveknek a tesztelése is elkezdődhetett. Ennek során több mint száz tesztsofőr és tesztmérnök hatvan gépjárművel több mint négymillió kilométert tett meg. Egy-egy tesztjárműben nem ritkán 250 mérési pontot is kijelöltek. A müncheni központ tesztpályáján különféle rázós útfelületeken, például egyenetlen macskakövön kínozták az oroszlánokat. Persze a tesztpilótákat kímélték, ezért fél óránként váltották egymást a fülkében. Csak itt harmincezer kilométert tettek meg a megújult TG-család tagjai. Kizárólag olyan újítások kerülhettek be a sorozatgyártásba, amelyek minden próbát sikeresen kiálltak. Így több ötlet is kiesett a rostán, de például a SmartSelect nevű forgókapcsoló megvalósulhatott.
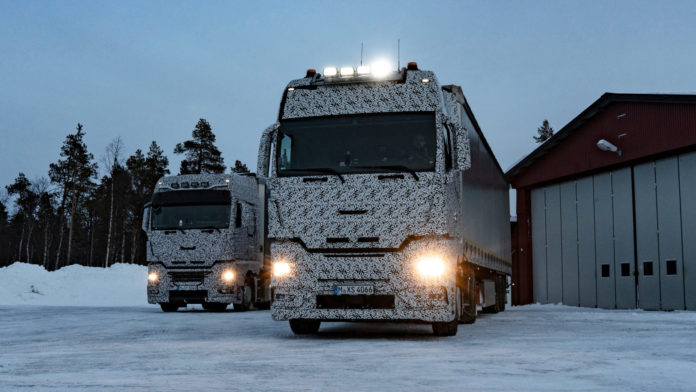
Kaptak hideget, meleget
A fejlesztés alatt álló MAN tehergépkocsikat persze közúti forgalomban is alaposan próbára tették. Spanyolországban tűző forróságban, míg Svédországban -45 Celsius-fokos fagyban, havas és jeges utakon tesztelték ezeket minden évben hosszú hónapokon át, teljes terheléssel és üresen egyaránt. Különösen nagy figyelmet fordítottak arra, hogy a különböző rendszerek hogyan működnek együtt a legváltozatosabb körülmények között. Például így végezték el az oldalsó holttérfigyelő rendszer radarjainak a kalibrálását annak érdekében, hogy gyalogosok vagy kerékpárosok érzékelésekor megbízhatón figyelmeztessen a rendszer, de például a hirdetőoszlopokat ne jelezze. Továbbá így biztosították, hogy a sávelhagyásra figyelmeztető rendszer kamerája a különböző országok eltérő útburkolati felfestéseit is megbízhatón felismerje. A tesztek során pedig az igazgatótanács tagjai is a volán mögé ülhettek, hogy saját maguk is érezzék a fejlesztések eredményeit a gyakorlatban.
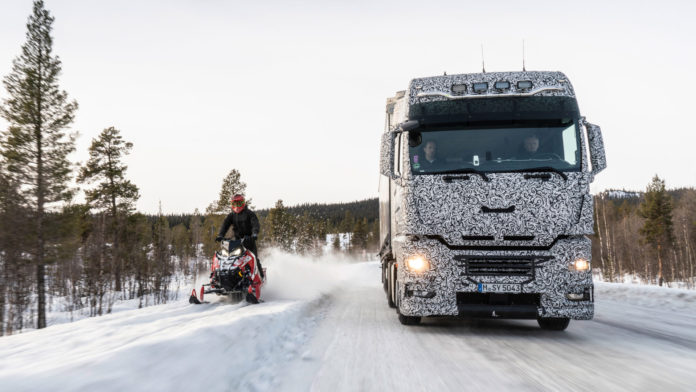
Korszerűsített gyártás
Majd 2019 márciusában már a megújult TG-család első előfutára is legördült Münchenben a szériatermelés gyártósoráról. A projekt részeként persze magát a gyártást is átfogóan továbbfejlesztették. Az MAN egyedül a müncheni üzemében egy több mint százmillió eurós beruházást hajtott végre, amelynek eredményeként akár napi ötszáz fülke is készülhet itt. Például a fülkéket összeállító új hegesztőcsarnokban az eddigi 47 helyett már 190 robot dolgozik, így lerövidült a termelés ciklusideje. Ezzel lépést tartva a fülkefényező részleget 85 millió euróból korszerűsítették, amely így már Európa egyik legmodernebb és legkörnyezetkímélőbb üzeme a maga nemében. Új eljárásként bevezették a szórással felvitt szigetelést, amely csökkenti a fülke belsőterének zajszintjét. Ezenkívül a steyri gyáregységben is egy új fényezőüzemet állítottak munkába, és a későbbiekben kizárólag itt fényezik majd az összes műanyag alkatrészt az MAN teljes termelési hálózata számára.
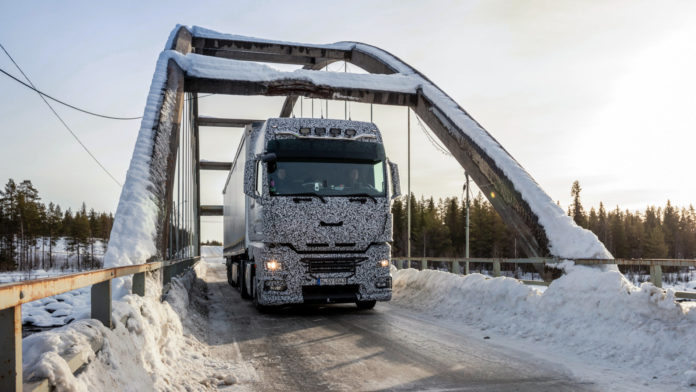
Az összeszerelő sort pedig 12 új munkaállomással bővítették ki. Mindeközben az MAN akadémiáján 1800 szerelőt képeztek ki a TG-család új gyártási eljárásaira. Ennek részeként ők is beülhettek a megújult modellekbe, ami remekül motiválta őket. Végül az utolsó finomításokat is elvégezve úgy a termékeken, mint a gyártási folyamaton, idén februárban minden szempontból sorozatgyártásra készen a nagyközönség előtt is bemutatkozhatott a megújult MAN TG-család.
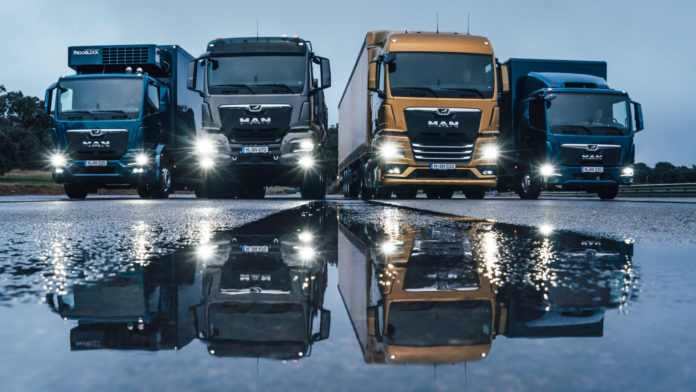